潜在失效模式及后果分析(Potential Failure Mode and Effects Analysis)是一门事前预防的定性分析技术,自设计阶段开始,就通过分析,预测设计、过程中潜在的失效,研究失效的原因及其后果,并采取必要的预防措施,以避免或减少这些潜在的失效,从而提高产品、过程的可靠性。
FMEA,是从可靠性的角度对所做的设计、过程进行详细评价。
知识准备
- 失效(Faiure):指产品丧失规定功能的状态,又译为故障。
- 失效模式(Failure Mode):产品失效的表现形式。例如,线路短路等。
- 潜在失效模式(Potential Failure Mode):指可能发生,但不一定非得发生的失效模式,也即平常所说的“可能存在的隐患”。
- 潜在失效后果(Potential Effect of Failure):指潜在失效模式会给顾客(含外部顾客、内部顾客)带来的后果。
- 后果分析(Effect Analysis):研究潜在失效模式发生后给顾客带来的危害性有多大。危害性可用三个方面来衡量:失效模式所产生后果的严重度、失效模式起因发生的频度、失效模式起因不可探测的程度。
- 后果(Effect):又译为“影响”。所以“失效模式及后果分析”又称为“故障模式及影响分析”。
DFMEA(Design FMEA)
设计FMEA是在设计过程中采用的一种FMEA技术,用以保证已充分地考虑和指明设计中各种潜在的失效模式及其相关的起因/机理,并就此在设计上采取必要的预防措施。
DFMEA的特征
- 以产品的元件或系统为分析对象,用表格的形式,从低层次逐步向高层次分析。
- 原则上是全面分析。然而,全面详细分析所需工作量很大,因此对已有使用经验表明效果好的部分,可免于分析或者提高分析级别;反之,对新产品或研制内容较多的部分,则应详细分析。
- DFMEA由产品设计人员主持,生产、品管、使用等技术人员参与,DFMEA小组一般由5~7人组成。
- DFMEA是一个动态性文件,应根据设计变化或获得的新信息及时改进DFMEA。应定期对DFMEA进行评审,重点放在发生频度和探测度的排序上,产品改进、设计控制改善以及问题发生时,排序都可能变化。
- 应将DFMEA分析到的特殊特性、预防措施等体现在后续的产品设计工艺文件中,如产品图样、控制计划、作业指导书中。
DFMEA的用途
- 识别需采取预防措施的设计缺陷。
- 为制订或修改特殊特性清单提供依据。
- 为评价产品设计的可靠性及优化设计方案提供依据。
- 为制订产品试验计划,确定产品、过程质量控制方案提供信息。
- 为故障诊断、制订维修方案提供信息。
- 为维修性分析、安全性及危险源分析、故障源分析等提供依据。
DFMEA分析对象
- 新设计的产品、部件、系统。
- 环境有变化的沿用零件。
- 发生了变化的材料和零件。
- 有重大设计更改的部件、系统。
DFMEA分析的时机
DFMEA应在设计意图(设计意图中包含对产品功能、性能等方面的要求)最终形成之时开始,并贯穿在设计工作的全过程之中。在正式的产品图样完成之时或之前,DFMEA应全部完成。
DFMEA分析的过程和方法
参见书《IATF 16949 质量管理体系五大工具》第二版 P106-P127。
DFMEA相关图片
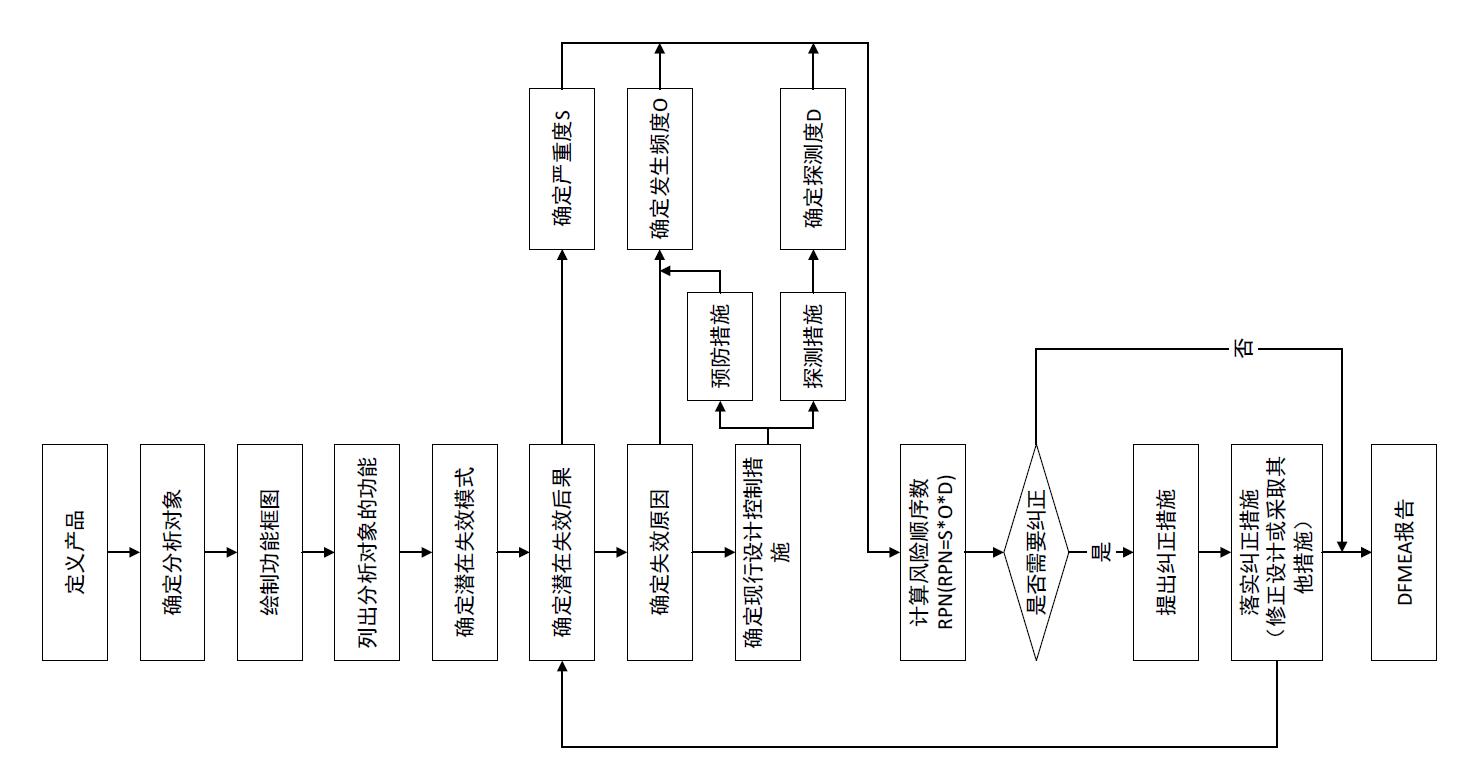
SOD表
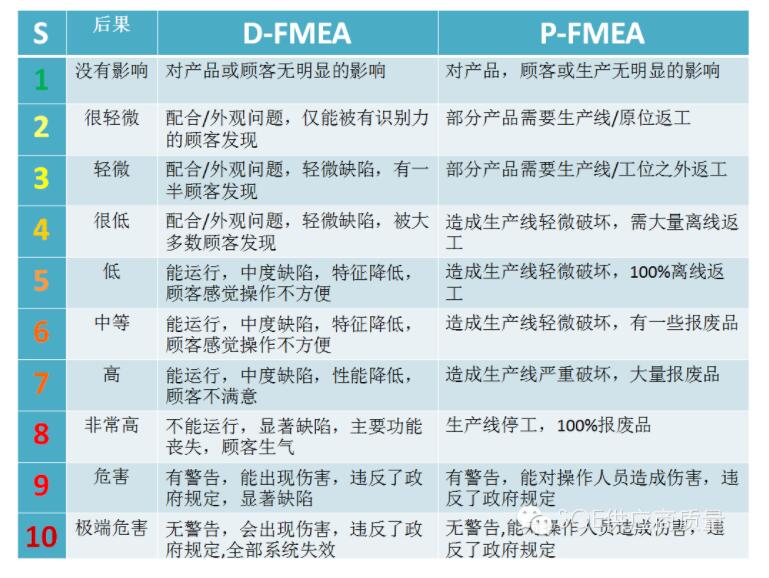
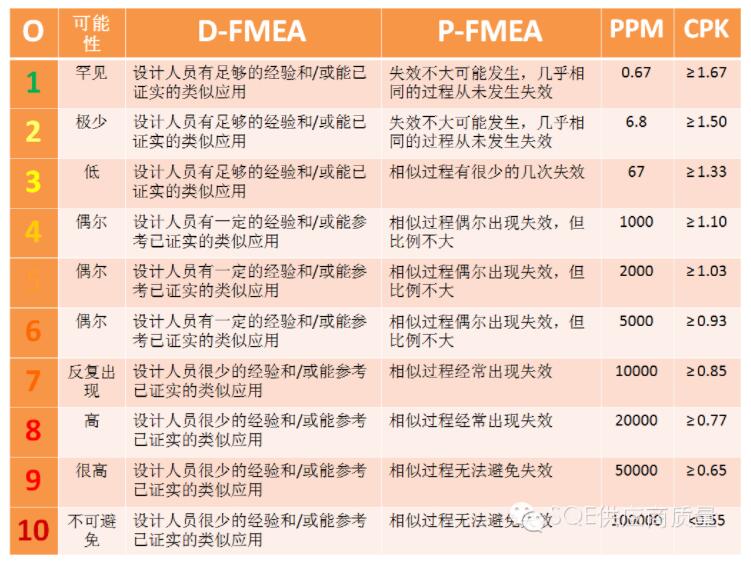
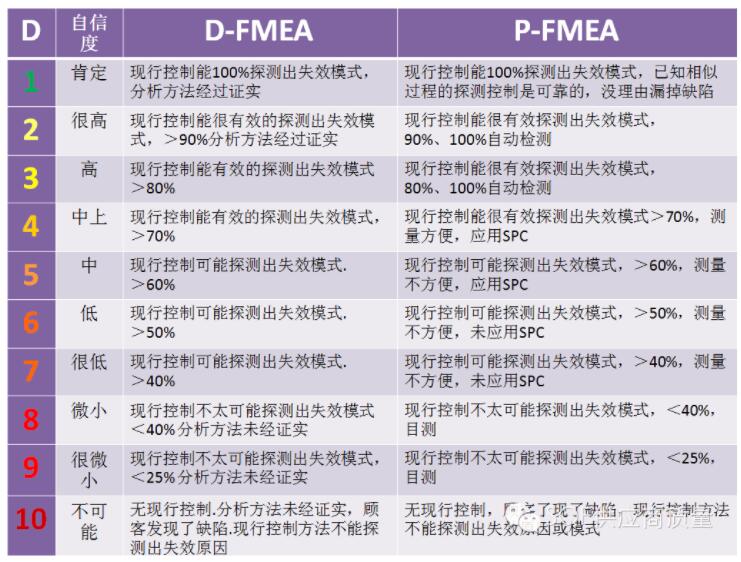